Join with us as we delve into some of the rare trades being safeguarded by Sovereign Hill's talented team of confectioners, wheelwrights and blacksmiths.
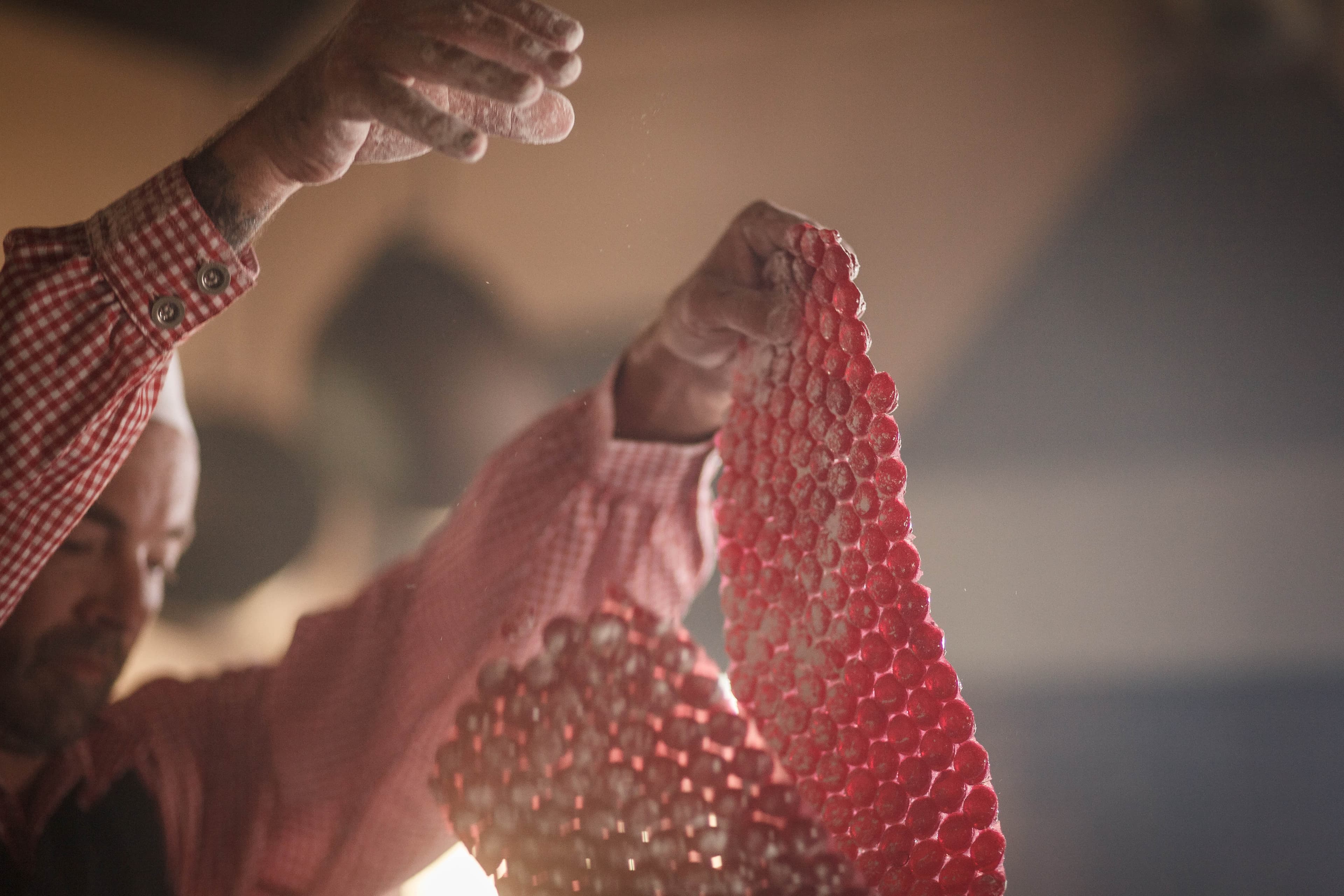
The lolly maker
If you’ve ever visited Sovereign Hill, there’s a good chance you went home with a jar (or two, or five) of raspberry drops. But have you ever wondered how they came to be?
To tell this story, we need to turn back the history pages to the bustling Victorian goldfields of the late 1850s. It was then that English immigrant John Brown first opened the doors of Brown’s Confectionery Manufactory after settling in the town of Dunolly (a small village north of Ballarat).
Following a devastating fire in the 1890s, the Brown family moved their business to Ballarat, where it operated until the 1970s. While operations ceased in 1974, the continuation of the art of sweet making in Ballarat never did.
When the business closed, the Brown family passed on their invaluable knowledge, recipes and equipment to the team at Sovereign Hill. Today, the confectionery team still use this original equipment and skills learned to make those famous handmade boiled treats we’ve all come to love.
The sweet-making process is an intricate one, but rather than try to explain this ourselves, we had Sovereign Hill’s head confectioner Ben Bignell give us some insight into this craft.
“Toffee used to make our sweets is heated to 160 degrees celsius. The toffee is poured out and kneaded by hand, before it is cut into pieces and hand-rolled through a confectionery roller,” he said.
“To get the colour red back in the day, they didn’t use artificial colours – they used cochineal red… extracted from the cochineal beetle. The good thing about the beetle was that it was odourless and tasteless, so it was pretty much perfect for confectionery making.”
While the beetle is not an ingredient you will see in the sweet making process any longer, Ben tells us he does have one secret ingredient.
“It’s not sugar, it’s the exact opposite. This is what is known as citric acid, so it adds the sour component to the raspberry drop,” he said.
Today, more than 32,000 jars of raspberry drops are made every year, just one of more than 40 different flavours available from Sovereign Hill’s Brown Confectionery.
When you’re next at Sovereign Hill, be sure to head along and watch the confectioners in action. You’ll find them tucked away in an alley just off Main Street.
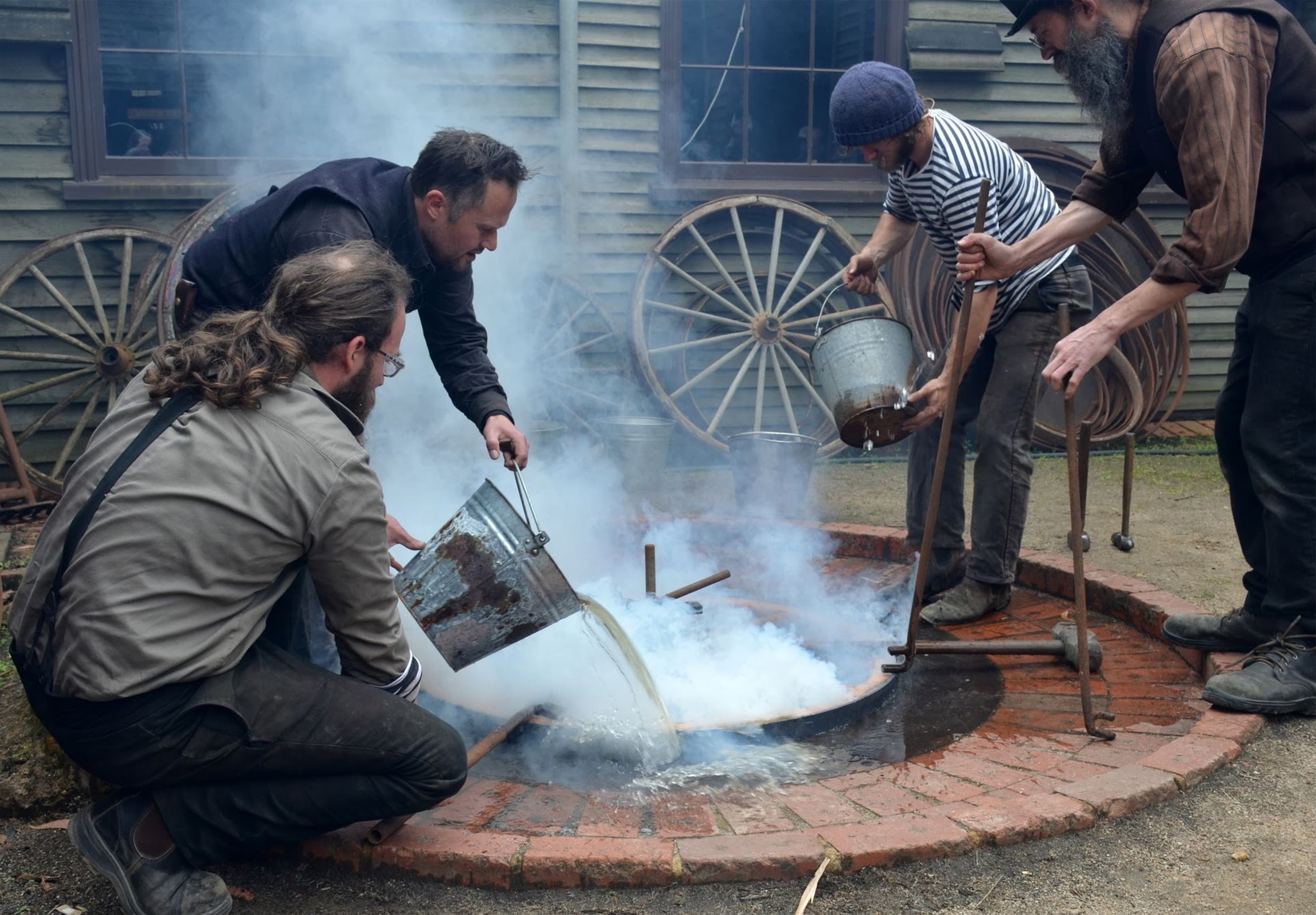
The wheelwright
If you were looking to get from one place to another during the gold rush, the easiest and most efficient way to get around was the horse-drawn carriage. Think of it as the taxi of the goldfields.
But unlike today, carriage drivers didn’t have the luxury of calling for a tow truck when they damaged their vehicle after hitting a pesky pothole. So, who did one call upon to fix their damaged carriage on the goldfields? The wheelwrights, of course.
But the job of a wheelwright was no easy feat – it took skill, engineering and a lot of training.
“The role of the wheelwright is vital to coach-making and there's a lot of attention to detail required,” says Mick Dando, Sovereign Hill’s wheelwrights and blacksmiths manager.
Unsurprisingly, there are very few wheelwrights still operating in Australia – making the job of the wheelwrights at Sovereign Hill an important one.
Step inside the wheelwrights and coachbuilding factory at Sovereign Hill today and you can see for yourselves the special skills required to build and repair horse carriages.
A recreation of the original W. Proctor Coachbuilder and Wheelwrights factory, which operated on the Ballarat goldfields, Sovereign Hill’s factory houses original machinery which is used during live demonstrations.
The demonstrations, which take place twice a day, draw a crowd fascinated by the skilled craftsmanship used in everything from wheel-making to timber-bending – a part of the job the wheelwrights enjoy so much.
“A lot of people don’t realise that the carriages at Sovereign Hill are actually made here and that we look after them, so there’s a huge satisfaction with sharing and showing our work with our audiences,” Mick said.
“They [the team] enjoy their public demonstrations where people watch them practicing their craft, like timber bending and hot tiring, which isn’t practiced in many other places.
“There’s also a great deal of responsibility that the team feels in ensuring that the information that they’re sharing is accurate. A major responsibility of the wheelwright team is to pass on their knowledge as much as they can, whether it be through demonstrations, workshops and training emerging wheelwrights.”
For Mick, the training and mentoring of apprentice wheelwrights means the next generation is supported to continue the unique trade long into the future.
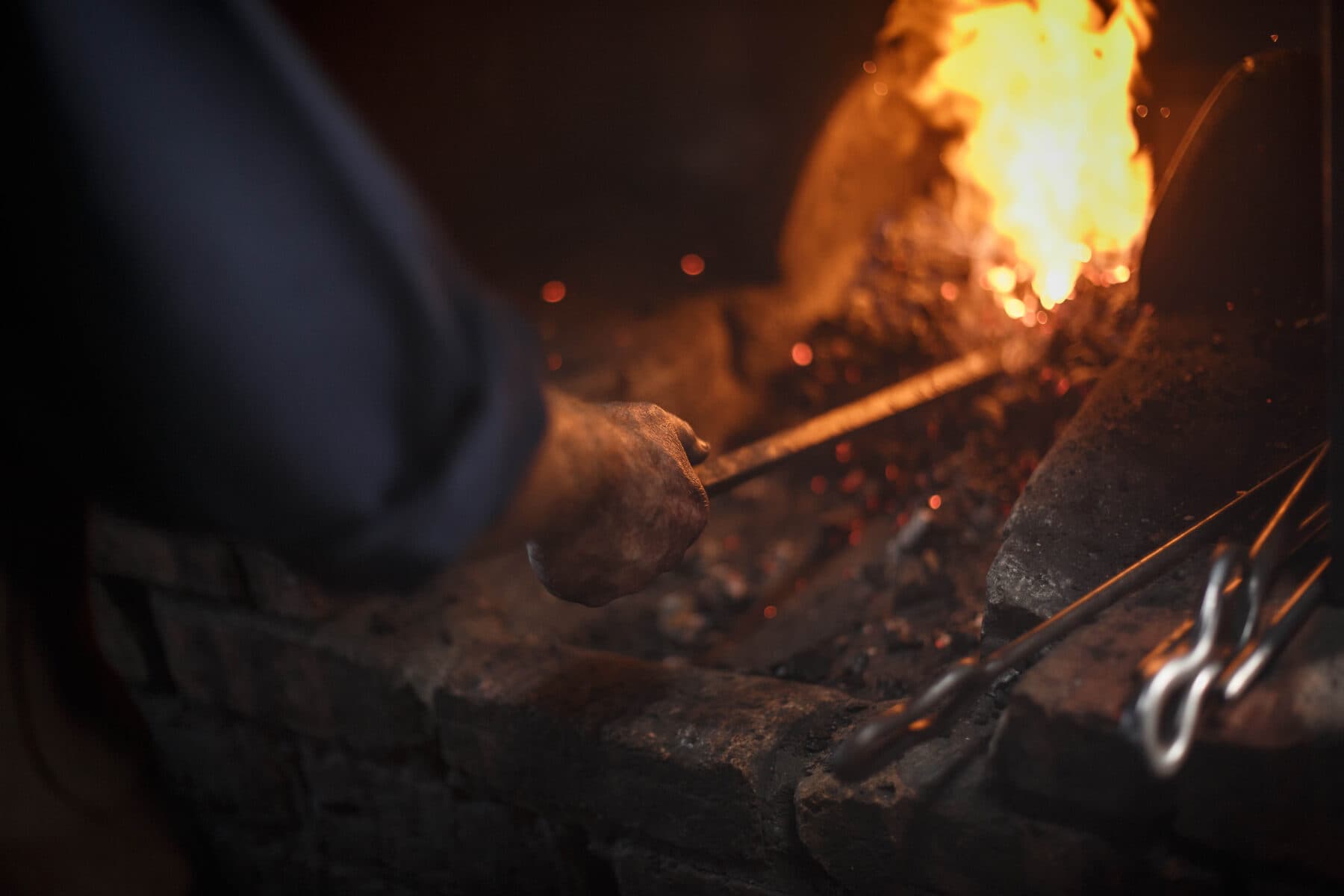
The blacksmith
Some of the most important people on the goldfields were blacksmiths.
Their ability to work and shape metal meant they were rarely short of money or work. Whether you needed your mining tools sharpened or crockery for your kitchen, it was the blacksmith you went to.
By 1857, there were at least 25 blacksmiths working on the Ballarat goldfields. But as mining for materials deposited by rivers gave way to deeper quartz mining, the humble blacksmith was soon replaced by industrial foundries that could churn out more powerful mining machinery.
But despite this, the craft of blacksmithing does still exist. Continuing the trade, which has been passed down from the artisans of the goldfields, is Sovereign Hill’s team of blacksmiths.
As he hammers hot metal by hand, blacksmith Tim Bignell shares some his knowledge of the story of blacksmithing in Ballarat with us.
“Not everyone moved to Ballarat to look for gold – for a lot of people, the gold rush provided more of a business opportunity. Quite often, it’s these people who made more money than people digging for gold, and a blacksmith was one of those people.
“It’s also a lot safer than digging holes under the ground. But of course, it is hard work and you do need certain skills. There is a lot of training that goes into becoming a blacksmith.”
Crafting everything from horseshoes and cooking pots to fire pokers and dust pans, a blacksmith heats their metal in a large furnace that can get up to 1,500 degrees celsius.
“You don’t need a lot of equipment to get yourself started up as a blacksmith, but one thing you certainly will need is a fire… you need that to get the steel hot before you can work with it,” Tim said.
You can watch Sovereign Hill’s talented blacksmiths in action at the G.M Dilges’ blacksmith shop, which is based on its namesake run by German immigrant Johannes Mathew Dilges and operated on Ballarat’s Main Road in the 1850s.